2024年6月
はじめに
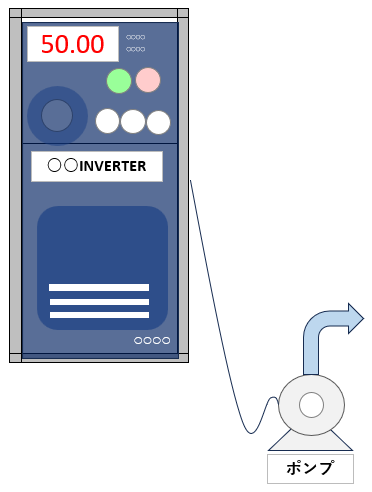
約6年前、関東地区の金属加工工場でポンプの更新工事を実施しました。この工事では、全てのポンプをインバータ制御に変更し、流量調整を従来のバルブ調整からインバータによる回転数調整に切り替えました。
制御面では、タッチパネルを用いて任意の周波数に変更できる機能や、ポンプの電流や圧力をリアルタイムで確認できるシステムも組み込み、より効率的な運用が行え、生産性向上が図られるようになりました。
消費電力等のデータは通常は記録に残せないのですが、「省エネでまこん(DEMS)」を導入し残せるようにしました。数年にわたるデータが時系列で保存されるため、必要な時にはすぐに読み出してその時の状況を再現したり、比較するなどエネルギー使用上の問題を見つける上でも大いに役立ちます。
さて本題です。当時、次のような省エネ対策を組み込みました。
「昼休みなどポンプは止められない」とのことであり、省エネのために自動で回転数を下げる機能を提案・組み込みました。
6年が経過しその効果がどうであったか、あるポンプ(11kW)について紹介します。
稼働状況
- 通常時48Hzで運転 休憩時は25Hzに下げる(自動制御)
- 休憩時間の合計は60分間(1日当たり)
- 実揚程・流量などポンプ特性は下方の図2を参照
省エネ効果
消費電力
・ポンプ回転数を48Hzから25Hzまで下げることで、消費電力は75%も削減できます。
4.84kW(48Hz)ー1.19kW(25Hz)=3.65kW 3.65kW÷4.84kW=0.75 75%の削減
削減電力量・電気代の実績は以下のとおりです。
・1日当たり、(4.84kWー1.19kW)×1時間=3.65kWh (休憩時間=60分/1日)
・年間では、3.65kWh×250日/年=730kWh (年間の運転日数は250日)
したがって、金額は730kWh×20円/kWh=14,600円/年 (単価は20円/kWhとした)
6年連続なので、730kWh14,600円×6年=87,600円/6年 (2018年1月~2024年1月)
・1日の削減電力量は下図をご覧ください。
30分のグラフにおいて、午前10時と午後3時の休憩及び昼休みは消費電力量が下がっています。
5分:0.1kWh/5分=0.1kWh×(60分/5分)≒1.19kWh
30分:2.42kWh/30分=2.42kWh×(60分/30分)=4.84kW
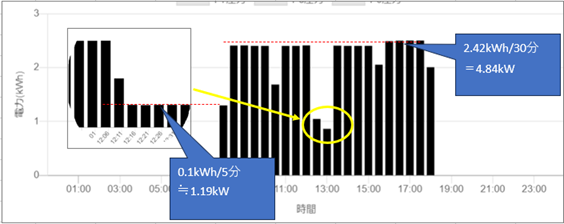
特性曲線
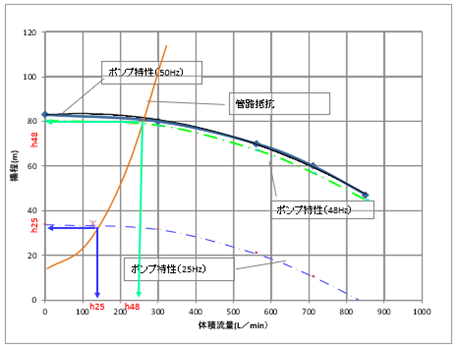
50Hzのポンプ特性はメーカーのデータシートから作成していますが、48Hz及び25Hzは独自に作成したものです。
ポンプ特性 | 48Hz運転 | 25Hz運転 | 備考 |
---|---|---|---|
消費電力(実測) | 4.84kW | 1.19kW | 48Hz→25Hzで3.65kW(75%削減) |
揚程(圧力より換算) | 約80m | 約30m | |
流量(特性曲線より) | 約250L/min | 約130L/min | 25Hz÷48Hz≒0.52→流量も0.52に半減 流量∝回転数 |
最後に
・ポンプの流量や圧力を最適化するためには、インバータ制御が極めて有効です。本事例のように応用的な運用方法を見つけることで、インバータ導入の効果をさらに高めることができ、省エネにもつながります。
・PLC内部データを記録に残したい場合にも「省エネでまこん(DEMS)」は使えます。
ただ単にデータを保存するためだけではなく、WEBブラウザから「日・月ごとの自動集計」や「その時の圧力はどうであったか」を再現するなどデータを共有できるため、活用の幅が広がると思います。